[8월 패널 토크] 패널들의 답변을 통해 궁금했던 점을 확인해 보세요! (37~79번)
페이지 정보
본문
37. Discrete 산업과 Process / Batch 제조산업에 스마트 제조 솔루션을 효율적으로 적용하려는 경우 각각 중점적으로 검토하고 점검해야 할 사항들에 대해서 질문드립니다.
[Siemens] Process/Batch 산업의 경우 일반적으로 석유화학, 식음료 산업의 형태를 띠고 있어 레시피 관리와 설비 운전조건에 따른 품질변화를 실 시간 모니터링 하는 것이 중요합니다. Discrete 산업의 경우에는 유연생산 체계를 구축하는 것이 중요합니다. 이러한 산업의 특성을 반영하여 산업군별 제품 포트폴리오를 제공하고 있습니다. 또한 지멘스는 디지털 트윈을 활용한 가상의 환경에서 사전 시뮬레이션과 검증을 통해 품질과 생산을 지속적으로 최적화 할 수 있도록 지원하고 있습니다.
[SAP] 제공해드린 SAP의 자료의 맨 마지막 표를 참조 부탁드립니다.
답변으로 말씀드리자면 공통으로 고려할 내용은 스마트제조라 하여 MES만 고려해서는 ‘안된다’ 입니다. 특히 가치 사슬 기준으로 보았을 때 최소한 계획-생산-설비-물류의 조합과 그 영향을 우선 검토 확인하여야 합니다. 그렇지 않고는 전사적인 효과를 볼 수 없습니다.
38. 당사는 제조업으로써 스마트 공장 즉 공정별 자동화를 진행할려고 합니다 혹시 당사에서 진행할시 설치 및 구매비용에 대한 정보를 알 수 있을까요
[Siemens] 자세한 사항은 지멘스 인더스트리 소프트웨어로 문의 부탁드립니다. 02-2055-2016
[SAP] 구축 비용과 구매 비용 등은 고려하시는 Scope과 수준에 따라 굉장히 다양하게 구성이 가능하여 별도로 진단 등을 수행하고 정리 해야 할 것 같습니다.
39. 제조 과정과 재고, 물류와 시장에서의 수요까지 고려하여 지멘스 시스템 구성을 통해 제조 비용과 물류, 생산 원가를 얼마나 절감이 가능한지요? 코로나19, 러시아와 우크라이나 전쟁 환경에서의 큰 변화 요인은 어떻게 반영하여 분석 정확성을 고도화하는지요?
[Siemens] 지멘스 스마트 제조 솔루션 도입을 통하여 정량적, 정성적인 효과를 본 글로벌 기업의 reference가 있습니다.
40. 2022년 8월 이후로 글로벌 IT 시장에서 제일 많이 성장하고 발전할 것으로 예상하는 사업분야와 솔루션에 대해서 문의드립니다
[Siemens] 스마트 제조 솔루션 영역에서는 디지털 트윈 관련 영역이 많이 성장할 것으로 예상됩니다.
[SAP] 환경 영역일 것 같습니다. 각종 규제와 유럽의 움직임 등을 보면, 환경과 데이터의 표준화를 결합하는 시도를 하면서 규제의 성격으로 장벽을 마련하고 있습니다. 이에 각 기업 들은 보고와 관리를 의무화 하게 되면서 시스템의 구현을 검토 하는데 Back end 프로세스가 적절치 않아 애를 먹고 있습니다. SAP의 오늘 발언 기조에서도 느끼셨듯이 기업 내부 뿐 아니라 외부와의 정보 교류 공유를 통한 Smart화를 이야기 합니다. 따라서 이러한 규제 등은 쉽게 해결 할 수 있는 형태가 되겠습니다. 역시나 이를 활용한 솔루션은 SAP에서는 이미 공급하고 있구요.
41. smart factory를 기업에서 도입하고 적용하려는 경우 경험하게 되는 문제점이나 애로사항들을 효율적으로 해결할 수 있는 방법에 대해서 질문드립니다
[Siemens] Why, what, how 관점에서 사전 목표 선정이 중요하며, 이에 따라 지속적인 모니터링이 중요합니다.
[코오롱베니트] 대부분 기업에서는 Master Plan을 기반으로 Smart Factory에 대한 투자를 계획하고, 실행합니다. 이러한 빅뱅 형태로 수행 시 문제점은 사전에 모든 과업을 정의하고, As-Was 분석을 수반하는 과정이 있으며, 이는 실제 도입이 되었을 때 고려하지 못한 부분에서 발생하는 문제에 대해 대처하기 어렵습니다. 코오롱에서는 Smart Factory와 관련한 부분은 Agile하게 작은 단위의 문제 해결 단계(문제인식 > 문제정의 > 데이터 분석 수행 > 효과성 검증 > 확산)를 거쳐, 투자의 대한 방향성과 효과성을 검증해 나가며 확산하는 전략을 추천하고 있습니다. 먼저 분석을 진행하여 우리에게 부족한 Data가 무엇인지, 우리가 이를 위해 취할 수 있는 투자나 해결 방법은 어떤 것인지를 고민하고 실행하는 단계를 여러 번 수행 하게 된다면, 자연스럽게 현장 개선의 확산이 이루어 질 것으로 예상합니다.
[SAP] 대표적으로 아래 그림의 붉은색 점선에서 문제를 경험하실 겁니다. 단계별 핵심요소 첨부합니다.
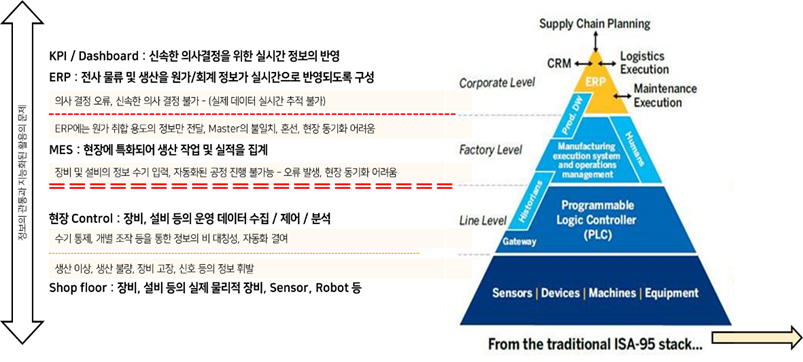
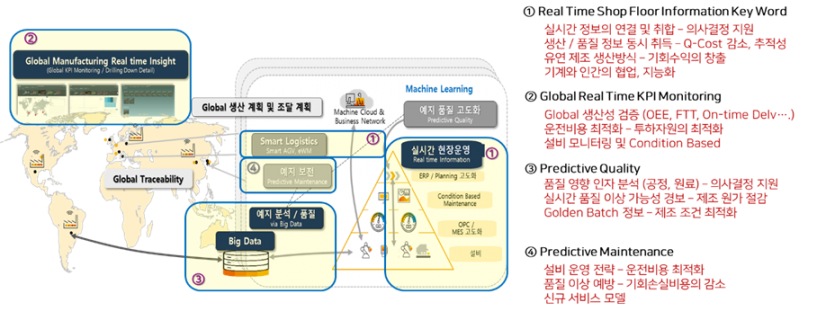
42. 생산성과 품질 향상 효과를 향상시키기 위해, 전 영역의 데이터 연결과 분석이 꼭 필요한 것인지, 설비쪽 디지털화만으로는 효과가 미약한지 궁금합니다.
[Siemens] 현장에는 조직 간의 연결성과 종속관계를 가지는 데이터가 많습니다. 이런 정보의 경우 변경점이 발생하면, 연관 데이터에 변경점이 전파되지 않아 실패 비용이 발생하는 사례가 있습니다.
[코오롱베니트] 생산성 향상을 위해서는 이의 분석과 추적을 위해 4M 1E 관점에서 고민해 보시고
품질과 생산성 관련한 문제의 발생 원인이 5개(Man, Machine, Material, Method, Environment)중 어디에 초점을 두어야 하는지에 따라서 데이터 연결 범위를 정해야 할 것 같습니다.
설비 쪽 디지털화만을 추진 하면 원인인 X인자와 결과인 Y인자가 모두 설비 데이터 안에 있을 때 인과 관계를 규명할 수 있을 것 같습니다. 인과 관계 규명을 위해 필수적인 데이터가 무엇인지를 먼저 고민 하시고 디지털화 대상을 선정 하는 것이 바람직할 것 같습니다.
[SAP] 설비만의 디지털 화는 제품마다 달리하는 기준점에 대한 정보가 엮이지 않을 것으로 봅니다. 설비 보전을 위한 정보로만 활용될 가능성이 높습니다. 또는 단순 시계열 정보 놓고 분석하려 하실 텐데 결국 전처리 등을 위한 매몰비용이 발생할 가능성이 매우 높습니다.
43. 스마트 제조 솔루션을 도입한 회사 중 제조원가 산출 정확도가 높아진 사례가 있을까요?
[Siemens] 해외 자동차 글로벌 리더와 해외 전자/전기 제조사들은 정확한 원가에 필요한 기준정보를 구축하여 다양한 시나리오로 시뮬레이션과 설계변경에 따른 원가 모니터링 활동을 진행하고 있습니다.
[코오롱베니트] 코오롱의 Connected Factory를 적용한 플랜트의 경우 센서에서 수집한 다양한 수불 정보를 활용하여 반제품 월말 배분율을 디지털화 전 10%~12% 조정에서 0%로 조정이 필요 없습니다. 실시간 공정에서 취득 되는 공정 데이터를 활용하여 품종 간 원가 차별성 확보도 가능합니다.
[SAP] 당연히 제조원가에 대한 산출 정확도가 높아집니다. 기본으로 3M (Man. Machine, Material)에 대한 정보를 활용하기 때문에 세분화된 원가 정보를 산출 할 수 있습니다.
필요하다면, Lot Size 1으로 극대화시켜 개별 원가를 산출할 수도 있겠지요. 허나 그 노력에 대해 효과가 크지 않다면, 원가는 Lot 단위 또는 제품 단위, 로지스틱스는 개별 단위로 운영하는 형태의 프로세스 구현도 가능합니다 .
44. 스마트팩토리를 하면서 ESG경영부분과 연계될수있는 부분도 있는지요?
[Siemens] 최근 화두가 되고 있는 ESG 경영의 경우 제조에서는 특히 기후이상과 관련된 탄소중립과 상당히 밀접하게 관련되어 있습니다. 지멘스는 디지털 트윈 기반의 플랫폼으로 탄소배출 절감과 탄소발자국 추적이 가능한 제품 포트폴리오를 제공하고 있습니다.
[SAP] ESG가 필요로 하는 정보는 기본적으로 가장 핵심이 제조 공정입니다. 원료 수급 정보와 투입 정보 그리고 거기에 수반하는 공정의 에너지 정보 등의 정보를 기본하여 ESG 리포트를 작성하게 됩니다. 현재까지는 정보 수집이 어려워 단순 Formular로만 해도 인정이 되나 향후에는 좀더 자세한 단위와 정보를 요구하게 되는 Phase 2~3 까지 간다면 Smart 제조는 필수 사항이 되지 않을까 합니다.
45. 지멘스의 솔루션이 SW 개발도 포괄하는 것으로 알고 있는데 최종적으로 소스 코드를 자동으로 생성하는 영역까지 완전하게 연결될 수 있는지 궁금합니다. 만약 그렇다면 구체적인 솔루션/도구 예시들 들어주시면 좋겠네요.
[Siemens] 지멘스의 Polarion이 S/W 개발을 지원하는 도구로 활용하고 있으며, 기능 단위 소스 코드와 테스트 케이스를 자동으로 생성하여 코드 개발 생산성을 높이고 있습니다.
46. 코오롱) 분산되어있는 data를 시계열로 연결했다고 하셨는데요, data를 한곳으로 집약하면서 표준화시켜 시계열로 모은 것인가요? 아니면 각각 DB단의 key만 맞추고 연결을 한 것인가요?
[코오롱베니트] 시계열 데이터로 모은 다는 개념 보다는 연속되는 시계열 데이터의 언제부터 언제까지가 어떤 오더와 연계 되는지, 어떤 원료를 투입했는지, 작업자는 누구이고, 어떤 제조조건을 사용하였는지를 등 다양한 메타 데이터를 연결하여 인과 관계를 규명하는 것을 의미합니다. 코오롱에서는 이러한 데이터를 중복 해서 통합 저장하지 않고 기존 정보 시스템과의 연결을 통해 상황에 필요한 Dataset을 추출합니다.
47. 스마트 팩토리의 전환을 1안:기존 데이터와 시스템을 분석 보완하여 전환하는 것과 2안:새롭게 데이터 중심의 시스템으로 전환하는 것 중 어느 안이 비용과 효율성을 고려하여 SAP,지멘스,코오롱 베니트에서의 추천 방안은 어떤 것일지요?
[Siemens] 기업이 처한 환경에 따라 다를 수 있습니다
[코오롱베니트] 베니트에서는 생산 현장의 업무 시스템 전체를 바꾸는 것은 현장 프로세스 많은 변화가 수반되므로 실현의 한계가 클 것으로 예상됩니다. 물론 현재의 시스템 수준에 따라 의사결정이 달라지겠지만 스마트팩토리 개념도 시대의 흐름에 따라 변해 가는 것이고 기존의 Legacy 시스템들도 현장과 함께 진화해 온 것으로 가치가 있다고 생각 되어 1안이 현실적이라고 판단 됩니다.
[SAP] 현장의 상황에 따라 다를 수 있을 것 같습니다만, 기본 원안은 2안을 중심으로 고려하지만 상황상 안되는 경우 1안으로 전환하는 것을 고려하시는 것이 좋겠습니다. 기존 시스템의 개선은 다양한 내용을 감안하지 않고 현장 최적화 관점으로만 설계되었을 가능성이 크기 때문에 한계가 있으리라 봅니다. 단기 성과 등 만을 고려하면 1안만 고민해도 되지만 분명 한계는 다가 옵니다. 그 시점에 매몰 비용 때문에 추가로 진행하기 어려울 수 있습니다.
48. 코오롱) data가 누적되면 어마어마하게 큰 사이즈로 나오는데 장기간 data 조회시 퍼포먼스 처리는 어떤걸 이용해서 하셨나요?
[코오롱베니트] 요즘은 시계열 데이터를 고성능으로 저장/활용 가능한 시계열DB(RTDB)가 오픈소스 또는 상용화 되어 제공되고 있습니다. 코오롱에서는 대량의 시계열 데이터를 가장 저렴하게 저장 활용할 수 있는 오픈소스DB 검증 및 최적화를 통해 활용하고 있습니다. 분석 목적에 맞는 Lot/Batch, 품질, 센서 데이터가 Connected Factory 관점으로 식별되면 유관 데이터만 수집하여 활용할 수 있는 체계가 완성 됩니다. 현재 코오롱은 이러한 식별 데이터를 기반으로 최소화된 데이터를 수집하여 분석에 활용하고 있습니다. 생산 실적 데이터는 MES에서, 시계열 데이터는 Historian 시스템을 통해 추출하여 필요로 하는 단위로 활용할 수 있는 체계로 되어 있으며, 분석을 위해 In-Memory DB를 활용하여 분석을 위한 마트로 활용하고 있습니다.
49. 코오롱베니트] ERP와 현장센서 데이터를 한곳에 모으지 말고 key 값만 가지고도 분석과 효과가 가능하시다고하셨는데, 좀 더 구체적인 사례를 들을 수 있을까요?
[코오롱베니트]
ERP: 오더 정보, 기준 정보, 원료 수입검사 결과, 품질검사 결과
MES: 작업 시간(작/끝), 작업자, 작업방법, 작업이력, 원료투입, 물류이동이력, 이슈발생기록 등
Historian : 초단위로 설비 설정값, 측정값, 제어값, 동작상태, 알람/이벤트 기록
이를 기반으로 ERP-MES-Historian을 연계 하여 어떤 오더별로 원료검사결과-원료투입량-작업자-작업방법-설비설정/운전이력-품질검사결과-물류이동경로-고객정보-이슈발생이력 등의 연계 추적이 가능합니다. 각 개별 시스템 (Legacy : MES, Historian, RMS, PLM, QMS 등)에는 이미 시스템 목적에 맞는 데이터가 존재합니다. 이러한 데이터들을 활용하기 위한 통합 관점의 Key와 인과 관계를 식별하고, 공정의 제어 인자와 계측 인자를 공정 프로세스에 맞게 정비하여 활용할 수 있는 Data 연결 구조를 만들고, 필요할 때 마다 이러한 데이터를 분석계로 가져와서 분석을 수행하는 선 순환 구조를 만드는 것이 중요합니다. 이러한 순환 구조가 안정화 되면 Data를 폭발적으로 활용하기 위한 시스템(Data Lake, 분석계)에 대한 투자를 추진하여도 늦지 않다고 생각합니다.
50. 스마트 제조 솔루션을 도입할 경우 가장 먼저 고객사에서 준비해야 할 사항은 무엇인가요? 가량 Data의 수집이라면 어떤 준비를 해야 하는지?
[코오롱베니트]코오롱은 데이터 초도 데이터 분석을 통해 연결되지 않은 데이터, 정제되지 않은 데이터로 효과성과 필요 사항을 점검하고, 우리에게 필요한 데이터가 무엇인지 진단을 하는 과정을 자연스럽게 수행하는 프로세스를 가져가고 있습니다. 그리고 나서 DT 전환을 위한 현황 진단이 필요합니다. 무조건 모든 설비에 센서 데이터를 취합하기 위한 시스템을 구축하기 보다, 효과성이 있을 법한 곳에 투자를 하기 위한 전략이 필요합니다. 데이터 수집 -> 축적 -> 분석 수행 -> 효과성 확인을 통해 투자의 정당성을 확보하여 확장 전개하는 것이 효율 적이라 생각 합니다.
[SAP] 현재 프로세스의 검토, 목적은 무엇인지, 무엇을 할건지, 어떤 효과를 기대하는 지 등을 정리 해야 합니다. 그리고, 할 수 있는 것은 무엇인지 검토해야 하며, SAP의 Industry 4.Now Program을 통해 Insight와 방향을 정할 수 있습니다. 아래 링크로 진단 해보시고 결과를 SAP와 같이 논의 하면 좋을 것 같습니다. Industry 4.Now 디지털 전환 진단 평가 (sap.com)
51. 많은 제조사들이 스마트팩토리와 자동화솔루션들을 도입추진하고 있습니다. 세분이 생각하시는 스마트팩토리+자동화 도입후 그 효과를 어떻게 표현하는게 좋을지 의견 듣고 싶습니다.
[Siemens]스마트팩토리나 자동화가 그 자체로 스마트 제조의 목적은 아닙니다. 결국 기업들은 스마트팩토리+ 자동화를 도입하여 제품개발 리드타임과 생산성, 품질이 얼마나 향상되었는지로 그 효과를 다루어야 합니다.
[코오롱베니트] 많은 사람들이 스마트팩토리는 자동화와 같은 개념으로 보는데 코오롱에서는 자동화(Automation)의 개념보다 자율제어(Autonomouse) 개념으로 정의 하고 있습니다. 단순하고 반복적이고 위험이 수반되는 작업의 시퀀스, 피드백 제어는 Industry 3.0의 개념 속에 포함되어 있다고 생각되고 AI나 머신러닝 기술을 활용하여 어떻게 운영하면 생산속도, 품질, 유연한 생산, 원가절감이 이루어질 것인지 작업자에게 가이드 해 주거나 의사결정을 할 수 있는 공장을 스마트팩토리라고 정의하고 있습니다. 예로 여러 생산현장에서 현장의 다년간의 운영 데이터 분석을 통해 불량이 발생하는 패턴을 인지하고 이를 회피할 수 있도록 능동적으로 제어하거나 작업자를 가이드 해주는 사례가 많습니다.
[SAP] 오늘 발표한 내용 중 L사의 사례 표를 참조하시면 좋겠습니다. 정량 효과 최대한 뽑을 수 있으면 좋으나 사실 정량 효과 뽑기가 쉽지 않으므로 개선 기대 효과에 이전 이후로 표시 하고 산정된 항목에 대해 최대한 금액 기준으로 산정해서 표현 하시면 좋겠습니다. (내부용)
외부는 그러한 정보를 공개하기 쉽지 않은 경우 심플한 정보 (% 내지는 몇배) 정도로 표시 하시면 좋을 듯 합니다.
52. 스마트팩토리가 각 회사의 환경(자금+인적역량+데이터 확보)에 따라 다를텐데 자율주행차의 Level 구분과 같이 스마트팩토리에 대한 레벨 구분이 되어 있는게 있는지 궁굼합니다.
[Siemens] 자율 주행차와 같이 스마트 팩토리 영역에서도 “스마트 팩토리의 수준 진단”이라는 단계별 수준 정의 기준이 존재합니다.
[SAP] SAP의 Industry 4.0 Maturity Assessment를 활용하여 현재 수준을 확인해 보세요.
SAP에 연락 주시면 간단히 현재 수준을 진단해보고 확인 할 수 있는 링크를 보내 드리거나 같이 답변을 달고 결과를 해석 논의 할 수 있는 자리를 만들겠습니다. Industry 4.Now 디지털 전환 진단 평가 (sap.com)
53. 기존에 구축한 자동화 설비와 센서, MES와의 통합은 얼마나 지원 가능할까요?
[코오롱베니트] 솔루션 업체에서 보통 “Industry 4.0 의 통신 표준은 OPC UA 이다” OPC를 지원하면 모든 설비 연계가 가능하다는 표현을 많이 하지만 이미 구축된 현장의 설비들은 전혀 이에 대한 대응체계를 갖추고 있지 않습니다. 이보다는 현장 설비의 자동화 설비에 적용된 PLC, HMI에 연결 가능한 다양한 통신 프로토콜을 지원하는 Gateway 제품을 선택하거나 전문업체에 연계를 의뢰하여 현장 설비에 맞추어 통합하는 것이 현명하다고 판단 됩니다.
[SAP] 대부분 통합 및 적용이 가능 한 것으로 보입니다.
물론 Tag Address 정보를 확인하기 힘들 몇몇 설비 들이 있습니다. 이 경우를 제외하고는 대부분 통합 가능한 영역으로 보시면 되겠습니다. (MII와 PCO 및 SCADA/IPC와의 연결을 통해)
54. 지맨스에서 고려하고 있는 현재 우리나라 시장에서 스마트 제조솔루션을 더 발전시키기 위해 어떠한 전략을 가지고 계실지 궁금합니다.
[Siemens] 지멘스는 산업별 디지털 전환 전략을 수립하여 운영하고 있습니다. 국내 시장에는 글로벌 레퍼런스와 표준 구축 방법론을 적용하여 고객의 디지털 전환을 지원하고 있습니다.
55. 4차산업혁명시대에 스마트 제조 솔루션의 기능들중에서 현재 보완되거나 개선되어야 할 기능들에 대해서 질문드립니다.
[Siemens] AR 기술은 4차 산업혁명 시대에 사람과 제조를 연결해주는 가장 중요한 요소라고 생각합니다. 현재 단계에서는 출시된 AR 하드웨어의 수준이 End-User의 UX 수준에 미치지 못한다고 평가되나, AR 하드웨어의 영역에 대한 추가적인 발전이 필요한 상황이라고 판단됩니다.
56. Smart Factory 실제 구현사례 통계로 볼 때, 기존의 전통적인 MES 대비하여 경영진에게 가장 효과를 많이 본 점을 설명할 수 있을까요?
[Siemens] 전통적인 MES는 일반적으로 제조실행 영역에 국한되어 논의가 된다면, Smart Factory는 제품 개발부터 생산, 서비스까지 전 Value Chain Scope로 확장되고, 특히 지멘스는 가상환경 기반, 즉 디지털 트윈 기반의 시뮬레이션을 통하여 가상 환경에서 실제와 동일한 제조 환경을 설계하고 시뮬레이션하여 최적화된 방안을 도출하는 것입니다.
[코오롱베니트] 공정 분석을 통해 생산 스피드를 최대로 높이고 허용 품질 맞출 수 있는 최적의 건 도출 하는 것이 실행 레벨에서 가장 효과를 볼 수 있는 방법이라고 생각됩니다. Smart Factory 구축 초기에는 기존 작업자 주간에 의해 이루어지던 현장의 비효율이 여러가지 다양한 형태의 정형, 비정형 데이터로 확인 가능합니다. MES는 생산 실적을 주로 관리하는 시스템으로, 시계열적인 공정의 과정을 담아내지 못하는 한계가 있어, 공정 과정의 비효율을 시계열 데이터를 활용하여 진단하고, 해결 방향을 잡아가는 활동들을 진행해야 합니다. 공정내 필수적인 제어 요소들의 최적의 조건을 도출하여 적용하고, 이를 기반으로 다시 생산성 향상을 위한 Speed를 증가하는 선순환 활동을 통해 공정 개선뿐만 아니라 생산성 향상 관점의 현장 관리를 한다면 유의미한 결과가 도출 될 것입니다.
[SAP] 프로세스의 유연성 확보, 품질 추적성 극대화, CAPEX 추가 비용 절감 기대, 고객 만족 극대화, 생산성 효율화 확대 및 불량감소, 기계 설비 기준의 대량 생산 영역이라면, 분석을 통한 예지 품질, 보전 등을 위한 정보 확보 및 운용 등을 이야기 할 수 있겠습니다.
57. 지멘스가 다방면으로 솔루션이 워낙 방대한데, FA분야 솔루션의 장점은 무엇인지 궁금합니다.
[Siemens] 지멘스 FA 분야 솔루션의 가장 큰 장점은 수직적 통합(Vertical Integration) 입니다. 지멘스 FA 제품기반 수직적으로 통합하여 쉽게 호환이 가능하고 좀 더 다양한 정보의 취득이 가능합니다.
58. 기업에서 data 분석을 효율적으로 하여 불량 발생률을 줄이고 생산성을 향상시킬 수 있는 방안에 대해서 문의드립니다.
[코오롱베니트] 현장 Digital化 적용 시 설비 데이터를 연계하면 해상도 높은 공정 데이터를 쉽게 확보 할 수 있지만 품질 검사나 원료 수입 검사는 대부분 샘플 검사 실시로 데이터의 해상도가 낮아 공정데이터와 품질 데이터의 인과관계 분석의 한계가 발생합니다. 생산 현장의 설비 데이터 확보와 더불어 원료품질, 제품품질을 실시간으로 확인할 수 있는 기술 도입이나 개발이 수반된다면 품질 개선과 생산성 향상을 위한 인과관계 분석이 훨씬 원활하게 진행 될 것으로 예상됩니다.
기업이 생산 현장에서 데이터를 활용하여 수율을 높이거나, 불량 발생율을 낮추는 것은 생산 스피드를 임계 값까지 높이고, 이에 따른 품질 수율 안정화를 기반하여야 합니다. 이를 위해서는 생산 Speed별 최정의 공정 조건(Golden Recipe)을 구축하여야 이며, 이를 위한 기초가 바로 공정에서 발생하는 다양한 정형, 비정형 데이터를 의미합니다. 이러한 데이터를 축적하고, 이를 표준 Recipe로 활용하기 위한 다양한 활동을 전개해야지만 현장에서 의미 있는 생산성 향상의 결과를 가져올 것으로 기대합니다.
[SAP] SAP의 View는 아래와 같습니다.
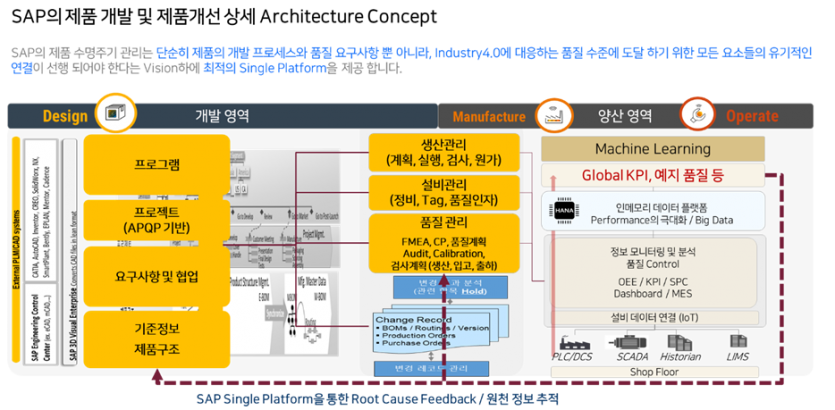
59. 분석 결과에 따른 보완까지 소요되는 기간은 통상 어떻게 될까요?
[코오롱베니트] 분석결과로 지목한 공정의 셋팅 값을 변경하거나, 설비를 변경하는 것은 현장 상황에 따라 상이합니다. 코오롱의 경우 Golden Recipe를 도출 2일 후 바로 현장에 적용하여 효과를 낸 사례도 있습니다.
[SAP] 그 부분을 최대한으로 줄이는 것이 관건이며, 시스템 적으로는 정보를 공유하고 빠르게 전파하는 기능이 최선일 것입니다. 이후는 사람과 프로세스 지요. 보고하고, 검토하고, 보고하고, 승인받고… 글쎄요. 얼마나 걸릴까요? 시스템으로 해결 안되지만 지연 등의 요인을 제거할 동인은 만들어집니다.
60. 스마트 제조 솔루션에 인재 모집을 위한 온라인 또는 오프라인 교육을 하실 생각이 있을까요?
[Siemens] 지멘스에는 솔루션에 대한 기본/심화 교육이 있습니다
[SAP] 최근 2~3년 사이 몇번의 온라인/오프라인 교육을 실시 하였었습니다. 현재는 수요에 따라 가변적으로 생각하고 있습니다.
61. 스마트 팩토리 구성 시, ESG경영 및 탄소 절감,re 100 등 기본적으로 솔루션에 포함되어 있는지요? 스마트 팩토리 구축 시 얼마나 비용이 추가된다고 보시는지요?
[Siemens] 지멘스 제품 포트폴리오는 기본적으로 디지털 트윈 플랫폼으로 가상의 환경에서 제품개발, 가상시운전 및 생산 시뮬레이션을 진행하여 탄소배출을 절감하고 있습니다. 또한 탄소발자국 추적을 위한 원가 솔루션(PCM)을 제공하고 있습니다. 스마트팩토리 구축 비용은 개별 기업이 처한 환경에 따라 상이합니다. 보다 상세한 구축비용이 궁금하시면 지멘스 인더스트리 소프트웨어로 문의 부탁드립니다. 02-2055-2016
[SAP] 네 SAP에는 ESG 및 Sustainability 솔루션으로 공급하고 있으며, 이를 제조 솔루션 / ERP와 연계하여 데이터를 모니터링 및 운영을 할 수 있게 구성되어 있습니다. 당연히 추가 비용은 들어갑니다.
62. K 방산 업체가 최근에 결실을 맺게 되어 좋은 것 같습니다. 방산 업체와 관련하여 스마트 팩토리 구성 시 중요한 고려 사항은 무엇이고, 구축 사례가 혹시 있는지요?
[Siemens] 방산은 제조의 영역이 납품에서 끝나는 것이 아니라 각국의 무기 체계와 연관되어 단종까지 Long-term 지원 체계 구축이 필요합니다. 지멘스는 K-방산업체와 다양한 협업을 진행하고 있습니다.
[SAP] 방위 산업은 특히나 추적성 즉, Genealogy(계보)라고 하는 정보가 매우 중요합니다. 또한 FAI, Redline Change와 같은 특수한 특성을 가지고 있어 생산의 주요 솔루션이 기능을 제공해야 합니다. 또한 재무/원가 적인 관점에서 호기 별 개별 원가법을 적용해야 하나 생산 구조상 Lot 생산을 해야 하는 반제품 등이 많은 것이 특징입니다. 이러한 방위산업의 특성을 고려한 재고관리 및 원가에 대한 관리 등이 수반된 제조 시스템이 고려되어야 하고, 설계 변경에 대한 영향 분석 및 형상연동 등이 관리될 수 있는 시스템이 수반되어야 합니다.
SAP는 이미 항공 및 방위산업에 특화되어 있는 스마트 제조 솔루션을 20년이 넘게 제공하고 있으며 주 사용 고객은 제너럴다이나믹스, 록히드마틴, 보잉, 에어버스, General Atomic, United Launch association 외 다수의 미국의 방산업체가 ERP PS의 GPD라고 하는 기능과 함꼐 사용하고 있습니다. 현재는 해당 솔루션이 너무 오래되어서 S/4HANA 내에 Embedding된 형태로 새로 Renewal 하여 솔루션을 제공해 드리고 있으며, 이름은 PEO (Production Engineering and Operation) 라고 부릅니다. ETO에 특화되어 있는 솔루션이며, SAP의 MII 및 BTP Platform의 최신 기술 등을 결합하여 활용 가능하도록 구성되어 있습니다.
PEO로 항공/방산 부분에서 가장 최근에 생산 영역의 구축을 완료한 고객은 일본의 가와사키 중공업, 미국의 Newport News Shipbuilding, General Atomic, Middle river Aerospace system 등이 최근 1~2년 내에 구축을 완료하였습니다.
63. 스마트 팩토리 관령솔루션을 구현할려면 주로 공장의 현장일 텐데 인력 감축등의 우려를 표명하여 반대에 부딪칠 경우 극복한 사례 및 방법이 있을가요
[코오롱베니트] 저희 회사에서 스마트팩토리는 자동화를 통해 인력 감축을 목표로 하고 있지 않습니다. 단순하고 반복되고 위험한 작업은 당연히 자동화를 통해 생산성을 높여야 하지만 현장에서 다양한 상황에 대한 유연한 대응은 아직까지도 사람이 하는 것이 훨씬 생산성이 높아 적정한 생산성 높은 자동화 진행이 필요하고 자동화 비율이 높아짐에 따른 잉여 인력은 부가가치를 높일 수 있는 데이터 분석, CPS 등 신규 기술 분야로의 전환 배치를 통해 지속적인 생산성 향상을 위한 선순환을 확보하는 것이 필요합니다. 현장의 기본적인 오퍼레이션은 체계화된 시스템을 적극 활용하고 현장 인력은 조금 더 성과가 높은 일에 집중할 수 있는 생태계를 만들어 간다는 컨센서스를 이루는 것이 중요합니다.
[SAP] 올해 Hannover Messe의 SAP Show Case에서는 상기와 같은 우려 때문에 완전 자동화보다는 협동로봇 등을 통해 작업의 효율을 극대화하는 방향으로 구성되어 있습니다.
방송 중에 소개 드렸던 L사 같은 경우도 주 작업은 사람이 합니다. (컨베어 방식에서 Cell 방식으로 전환 구현되면 이러한 기조는 더 강해집니다.) AGV 및 Tirebot 등 주요 로봇 등은 사람을 Support 하는 방식으로 구축되어 있습니다. 물론 Painting 같이 사람이 하기 힘들거나 반복된 고정된 작업을 하는 경우는 로봇 등으로 대체됩니다. 해서 SAP가 이야기한 Mass Customization/Mass Production을 위해서는 기계의 지능화도 필요하지만 결국 사람이 개입하도록 할 수밖에 없는 상황이 만들어지는 것이지요. 이런 기조는 독일이 노동과 자본집약 설비의 Trade-off를 상쇄시키는 주요 포인트 이기도 합니다.
64. 현재 생산/제조 현장에 AI가 적용된 부분은 주로 어떤 파트이며, 생산성 향상과 연계가 있는지 궁금합니다.
[Siemens] 지멘스는 인공지능 기술을 이용하여 다양한 분야에 활용하고 있습니다. 대표적으로 현재 장착되지 않은 센서 정보를 가상화하는 Virtual Sensing 기술에 폭넓게 활용하고 있습니다.
[SAP] 현재 SAP 내에 생산/제조 현장에 AI가 직접적으로 적용된 기능은 Visual Inspection을 제공하고 있으며, Predictive Quality를 통해 Machine Learning 기반의 품질 이상 징후를 판별하여 작업자에 실시간으로 알려주는 정도의 기능을 현재 제공하고 있습니다.
65. 디지털 트윈을 지원하는 기능이 있나요?
[Siemens] 지멘스 제품 포트폴리오는 디지털 트윈 기반 플랫폼으로 다양한 제품 포트폴리오를 제공하고 있습니다. 최근에는 NVIDIA와의 제휴를 통해 초연결/초실사/초지능의 산업용 AI 메타버스를 구현하고 있습니다.
[SAP] SAP에는 3D Visual Enterprise라고 하는 솔루션이 CAD 도면의 형상의 Authoring과 경량화를 담당하여 SAP 솔루션 전체에 제품 및 설비의 형상 정보를 제공할 수 있도록 구성되어 있습니다.
SAP 전체의 솔루션에는 해당 솔루션의 형상 정보를 볼 수 있는 Viewer가 내장되어 있습니다.
또한 제조 라인의 Digital Twin을 위해서 Digital Manufacturing Cloud 내에 Production Process Designer (Shop Flow Designer)라는 기능을 통해 제품의 생산 공정과 설비의 Layout 및 데이터의 흐름을 가시적으로 제어하는 형태로 실제 현장 정보의 가시성을 확보합니다. 이를 통해 설비에서 실적 정보 및 이상 정보를 보낼 때 후공정의 설비에서 어떤 데이터를 받을지, ERP에서는 어떤 처리를 수행할 지, 문제인 경우 어떤 일을 수행할 지 등을 Design 할 수 있도록 구성되어 있습니다. 이 두개를 조합하여 현장 전체 및 제품에 대한 Digital Twin을 구성 할 수 있습니다.
66. 기준정보가 다른 ERP,MES,PLM, QMS의 데이타를 어떤 기준으로 통합을 하나요? 이 데이타들과 시계열데이타와의 상관관계는 어떻게 해야 할까요? 데이타 Set의 조합이 이루어지지 않은 빅데이타의 분석은 의미가 없을것 같은데요..의견 부탁합니다.
[코오롱베니트] 개별 시스템 도입 목적에 따라 Silo화 되어 구축한 시스템에 저장된 Data를 활용하기 위해서는 출고하는 Lot이나 Batch를 기준으로 원부 원료, 공정, 품질 데이터를 트래킹 할 수 있는 구조로 만드는 것이 중요합니다. 각 단위 공정 별 생산실적 데이터와 공정에서 발생하는 시계열 데이터를 매핑하여 활용하기 위한 가장 기본이자, 근간이 됩니다. 이러한 Connected Data를 기반으로 데이터 분석 뿐만 아니라, 현장 통합 Data 운용 체계를 구축 하는 것이 핵심이라 할 수 있습니다.
[SAP] 예, 데이터 Set이 조합되지 않은 데이터는 사실 Machine Learning에서도 의미가 없습니다.
보통 이 경우 데이터가 유의미하게 조합되게 하기 위해서 전처리라는 작업을 수행하는데 이게 어마어마한 노력이 필요하며, 심지어 약간의 변수 변경에도 쓸모 없어지는 상황이 발생합니다.
해서 빅데이터 분석이라 일컫는 모든 작업의 대부분이 전처리에 소요됩니다. 그것도 아주 좁은 영역의 현상에 대한 분석을 점단위로 분석하게 됩니다. 그런데 문제는 연결고리가 시계열 밖에 없다면, 데이터의 입력 시점과 적용 시점으로 마킹된 정보 자체가 엉망이면 데이터 결과도 엉망이 되는 것입니다.
따라서 데이터의 분석을 위해서는 전처리에 노력을 쏟을 것이 아니라 적재되는 시점에 상호 연계성을 가진 데이터로 적재하도록 프로세스와 시스템을 바꾸는 것이 선행 되어야 합니다.
67. 메타버스 관련 새로운 모델에 대해 관심 있는데 자세한 설명이 되었으면 좋겠습니다.
[Siemens] 메타버스 모델을 강화하기 위하여 지멘스는 최근 NVIDIA의 옴니버스와 협업을 추진하고 있으며, 지멘스의 데이터 플랫폼을 연계하여 기존의 시뮬레이션 기능은 유지되지만, 보다 실제감 있는 메타버스 환경을 경험하실 수 있습니다.
[SAP] 아직은 Metaverse와 관련한 Business Level의 고민이 한국은 매우 적은 듯합니다.
세션 중에 잠깐 언급하였던 Out-come Based Revenue 등의 Concept을 기준으로 하는 Virtual Factory가 가장 가까운 모습이 아닐까 예상이 됩니다.
예를 들어보면, 특정 공장은 3D Printer를 가지고 서비스를 하고, 특정 공장은 설계, 특정 공장은 Painting Machine을 운영한다 가정해봅시다. 고객은 본인이 설계한 3D 도면을 블록체인 기반으로 IP를 보호받으면서 3D Printing과 Painting을 요청합니다. 이를 위해 Business Network 상에서 Sourcing을 수행하여 의뢰하고, 의뢰받은 공장은 의뢰자의 생산 및 판매계획을 공유 받아 본인의 생산 계획을 수립하고 공유합니다. Painting 공장도 동일한 과정을 수행하구요. 의뢰인은 Digital Twin화 되어 있는 공장의 현재 상태 등을 공유 받고 상황에 따라 가상 공간에서 회의 및 의사 결정을 수행합니다. 납품 시 PPAP / FAI 같은 내용도 작업 검사 결과에 따른 형상 정보와 문제가 있는 위치 등을 동시에 접속한 공간에서 형상을 공유하면서 품질관련 문제 등을 논의 합니다.
이러한 모든 행위와 물류의 흐름은 마치 하나의 공장 내에서 수행되는 것과 같이 운영되는 플랫폼이 메타버스의 하나의 모습으로 예상되며, 이를 위한 새로운 비즈니스 모델 등이 서비스의 형태로 창출 될 것으로 생각합니다.
68. 코오롱베니트 - 5G를 사용해야 할텐데 통신 비용이 너무 많이 들지 않을까요? 절감방안을 제시해야 합니다.
[코오롱베니트] 코오롱 공장 환경은 공장의 범위가 너무 넓고, 클린룸과 같이 폐쇄 공간이 많고, 통신을 위한 많은 장애물이 존재하여 5G 적용이 현실적으로 불가능 하였습니다. 아직까지 코오롱 공장에서는 전용 WIFI를 이용하고 있으며 향후 기술의 적정성을 고려하여 전환 할 예정입니다.
69. 지멘스 스마트팩토리 도입은 성공적이라고 들었습니다. 실제 활용 측면에서 이슈가 있는지, 없다면 어떤점이 효과가 있는지 궁금합니다. 그리고 디지털 트윈이라고 하는 영역을 잘 활용할 수 있는 방안이 어떤 부분이 있는지 문의드립니다.
[Siemens] 디지털 트윈 구축이 성공적이기 위해서는 먼저 “병목 구간이 발생하는 지점은 어디인지?” 등과 같이 목적 함수가 명확해야 합니다. 두 번째는 디지털 트윈의 활용도를 높여야 합니다. 이전에 디지털 트윈은 설계 시점에 활용하고 더 이상 활용되지 않아 투자 대비 효용성이 낮다고 평가되었지만, 최근에는 가상 시운전과 운영 시점에 현장의 문제점을 인지하고 의사결정을 내리는 용도로 활용도를 높여야 합니다.
70. Asset Administration Shell, OPC-UA 표준을 활용하나요?
[Siemens] 지멘스는 OT-IT 솔루션을 연계하기 위해 OPC-UA의 연결성을 지원하고 있으며, AAS을 이용하여 Asset의 스마트 제조 환경에 연결되고 Life Cycle 관리에 활용될 수 있도록 지원하고 있습니다.
[SAP] SAP는 Industry 4.0 Council의 주요 멤버이면서 AAS나 OPC-UA의 표준을 적극 활용하도록 솔루션을 공급하고 있습니다. AAS의 Concept과 같이 설비 등을 On-boarding하여 정보를 공유할 수 있는 Concept이 내장된 솔루션 등을 Asset Intelligence Network라는 솔루션으로 이미 공급하고 있으며, SAP의 주 권고 Protocol인 OPC-UA/DA 등을 가지고 처리 할 수 있도록 제조 솔루션에 Shop Floor 운용 기능을 내포하고 있습니다.
71. SAP S/4HANA를 public cloud기반과 PCE로 구축하는 것 중 구축이 어려운 것은 어느것이며 그 이유는 무엇인가요? 또 PCE와 온프라미스에서 ERP를 운영할 경우 장애 대응측면에서 어느것이 용이하며 그 이유는 무엇 때문인가요?
[SAP] Public Cloud와 PCE의 가장 큰 차이는 Implementation guide를 적극적으로 사용하냐 안하냐의 차이인 것 같습니다. 즉, Public Cloud는 시나리오 기반으로 BP를 적극 도입하고 그 안에서 셋업을 한다면 PCE는 기존 On-Premise와 동일한 환경과 구조로 Setting을 수행합니다. 따라서 PCE는 변수를 더 많이 고려해서 구현을 할 수 있고 Public도 비슷하지만 좀더 변형을 가하는 것이 어렵다 보시면 됩니다. 우리 회사의 프로세스가 변수도 많고 고려할 것도 많아서 복잡한 내용을 담아야 한다면 PCE, 아니라면 Public 이렇게 정리가 됩니다만 최근에는 Public의 유연성이 더 많아져서 큰 차이가 없어지고 있습니다. 가장 최근 구축 완료한 Bentley에 샤시를 제조 납품하는 공장의 경우 S/4HANA Public과 SAP의 DMC를 기반하여 Smart 제조 환경을 구현 완료하였습니다.
PCE와 온프레미스의 장애 대응 측면에서는 해당사의 IT 조직을 직접 운영하느냐 외부에서 운영지원 해 주느냐의 차이입니다. 장애 발생 시 모니터링 및 대응의 내용은 동일하다 하겠습니다.
서버나 인프라 측면에서 본다면, Hyperscale (AWS, Azure, Google) 등의 인프라를 사용하므로 대체로 고객사의 선호도 내지는 IT 운영 방향성에 따라 달라지는 것 같습니다.
72. 스마트 제조 솔루션은, DMC (Digital Manufacturing cloud)와 일맥상통하는 부분인가요?
[SAP] 네, 가장 중심에 있는 솔루션은 DMC이지만 SAP의 스마트제조 Concept은 좀더 넓은 그림으로 이해하시면 좋겠습니다.
73. 한국 제조 기업 중, SAP 의 스마트 제조 솔루션을 적용하는 기업이 있나요?
[SAP] 현재 몇몇 기업들은 도입하여 사용 중이며, 해외에 비하여 적은 것은 사실입니다.
허나 도입 고객의 경우 매우 좋은 결과를 얻고 있는 것으로 알고 있습니다. (V사 건설기계 등)
74. 아마존의 스마트 제조 (Smart manufacturing) 과 SAP 의 스마트 제조 솔루션은 가장 큰 차이점은 무엇인가요? 아마존과 확연하게 대비되는 SAP 만의 큰 강점은 무엇인가요?
[SAP] 아마존의 스마트제조는 저도 이번 하노버 메세에 가서 확인하였습니다만, 구체적인 솔루션이기 보다는 Platform에 데이터를 어떻게 적재할 것이며 연동할지에 대한 내용이 주를 이루었던 것 같습니다. 또한 Edge 등에 대한 내용이 많아서 Cloud와 Edge간의 연동의 내용이 주를 이루었던 것 같습니다. 즉, AWS위에 제조 솔루션을 어떻게 올리고, 운영할지 데이터는 어떻게 연결할지에 대한 내용이 Main이었으며, SAP는 구체적인 솔루션을 제시하면서 고객의 비즈니스 프로세스를 들여다봅니다. 기술 및 기능을 나열하고 고객 보고 알아서 하시라는 Concept이 아닌 프로세스와의 결합 특히 현장 물류 (JIS / JIT / KANBAN)와 제조 프로세스, 재고, 영업 등과의 연계를 고려한 프로세스를 제공하는 것이 가장 큰 확연한 차이가 아닐까 싶습니다.
아래 그림의 제조 프로세스 예시를 보시면 쉽게 이해가 되실 것이라 생각됩니다.
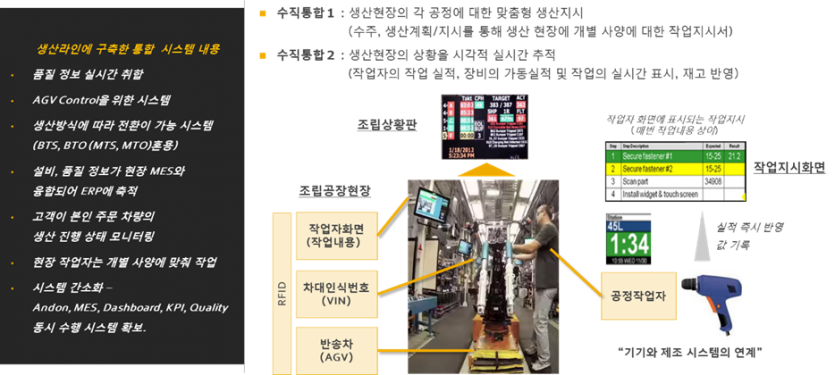
75. 정유 공장이나 석유화학 공장에 적용된 사례를 알고 싶습니다. 현장에 설치되는 스마크기기나 센서 등이 방폭설비 인증을 받은 제품이 있는 지도 궁금합니다.
[SAP] SAP의 파트너사들에게는 제공하는 다양한 스마트기기와 센서 등이 있는 것으로 알고 있습니다.
76. 요즘 SAP 프로젝트를 하면, 스마트 팩토리 또는 스마트 제조라는 개념이 많이 나옵니다. 실제 구현 사례에서 SAP만으로 커버되는 영역과 다른 솔루션이 필요한 영역이 있을 것이라 생각됩니다. 구체적인 사례로 설명 부탁 드립니다.
[SAP] SAP가 ERP만 제공하지 않습니다. 기업 전반에 걸친 모든 영역 (연구-영업-구매-계획-제조-재고-물류-설비-원가-재무-환경)에 대한 솔루션을 제공하고 있으며, 각 영역에도 고객의 상황에 맞게 적용할 수 있는 다양한 기능과 솔루션을 공급합니다.
재무 영역을 제외한 ERP의 기능과 솔루션의 조합은 아래와 같습니다.
77. 중소기업을 위한 스마트 제조 솔루션 제품이나 합리적 가격정책이 있는지 궁금합니다.
[SAP] SAP는 다양한 솔루션과 빠르게 적용 가능한 Light한 제품까지 폭넓게 공급하고 있습니다.
78. 스마트 제조라하면 요즘 회자되는 로봇에 의한 제조도 포함되는지요? 그럴 경우 초기투자비용 대비 성과를 낼 수 있는 좋은 프로세스가 있을런지요? (예: 국책지원 등)
[SAP] 로봇에 의한 제조도 스마트 제조의 한 영역입니다. SAP는 Production Process Designer라는 기능을 제공하여 설비간 정보 교환을 매우 수월하게 할 수 있는 기능을 제공합니다. (PLC 코딩 제거)
79. SAP 스마트 팩토리를 구현하려면, 기설치된 MES 에서 재활용 가능한 부분과 신규도입해야 하는 부분을 어떻게 구분해서 추진해야 하는지 개략적인 가이드라인을 설명해주시기 바랍니다.
[SAP] 아래 내용 참조 부탁드립니다.
- 이전글[8월 패널 토크] 패널들의 답변을 통해 궁금했던 점을 확인해 보세요! (80~93번) 22.08.19
- 다음글[8월 패널 토크] 패널들의 답변을 통해 궁금했던 점을 확인해 보세요! (1~36번) 22.08.19
댓글목록
등록된 댓글이 없습니다.